
Down to the Wire: How Boeing Uses AR in Assembly
Here’s a fun fact for you: about 130 miles of wiring go into every new aircraft.
Laying that wire requires high degrees of precision and leaves little margin for error. Traditional wiring instructions were provided via paper manuals packed with diagrams. Technicians had to move (mentally and sometimes physically) back and forth between the wiring site and the instructions.
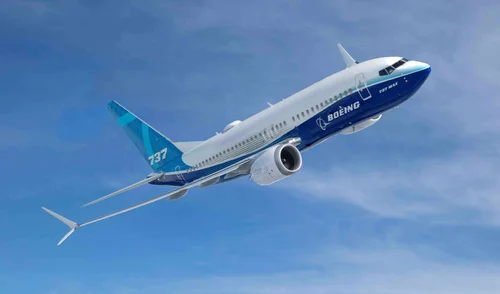
From AR Insider
In 2018, Boeing started testing augmented reality (AR) to provide technicians with real-time, hands-free, interactive 3D wiring diagrams.
“Traditionally technicians had to look at and interpret a two-dimensional twenty-foot-long drawing and construct that image in their mind and attempt to wire based on this mental model,” said Brian Laughlin, IT Tech Fellow. “By using augmented reality technology, technicians can easily see where the electrical wiring goes in the aircraft fuselage. They can roam around the airplane and see the wiring renderings in full depth within their surroundings and access instructions hands-free.”
Boeing implemented Google Glass with Upskill Skylight. Technicians can move through multiple instruction prompts using voice commands, Google Glass gestural taps, and a head-tracking interface. The voice-based approach allows technicians maximum dexterity and freedom of movement with all ten fingers.
Technicians can also bring in outside help—right into their line of site. They can call in a remote expert for “see what I see” support using Google Glass’s built-in camera and voice input. And they can stream how-to videos directly in their field of view.
Paul Davies, Boeing Research & Technology Associate Technical Fellow said, “Our theory studies have shown a 90% improvement in first-time quality when compared to using two-dimensional information on the airplane, along with a 30% reduction in time spent doing a job.”
Boeing Senior Manager Randall MacPherson said, “Wearable technology is helping us amplify the power of our workforce.” And the numbers prove it. Boeing cut production time by 25% and lowered error rates to nearly zero.